Contact Us
Mobile:
+86-17798188886
E-mail:
jxinxinye@126.com
Address:
Shiliangzhuang Industrial Zone, Gaoyi$®☆ County, Hebei Province, China
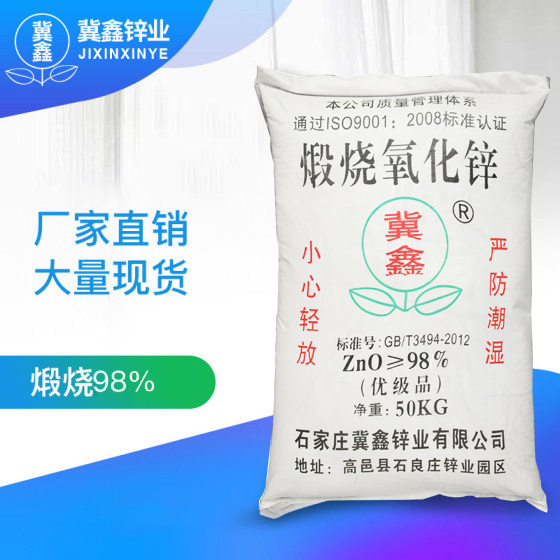
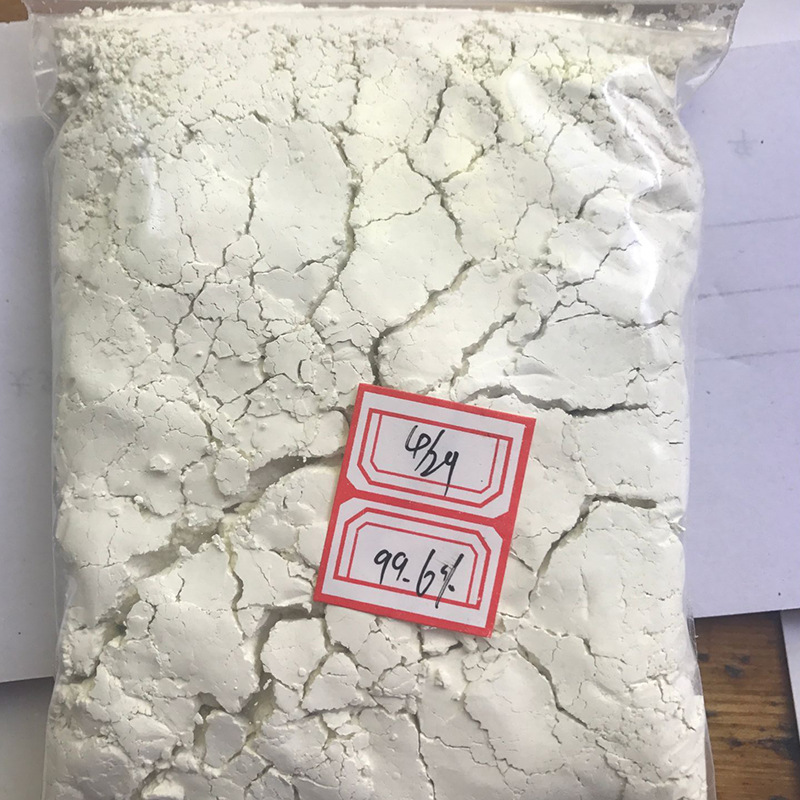
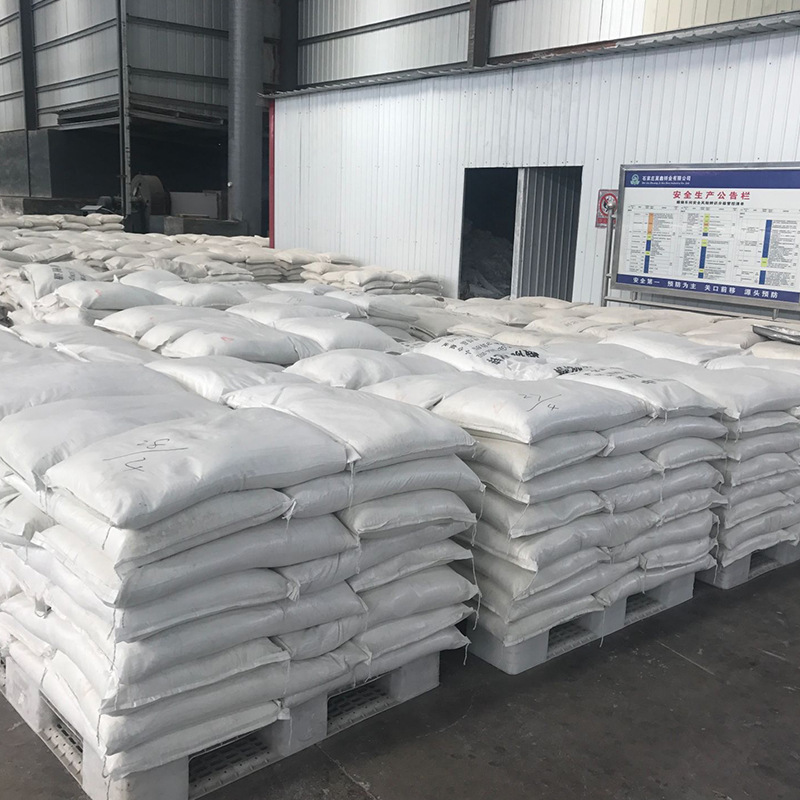
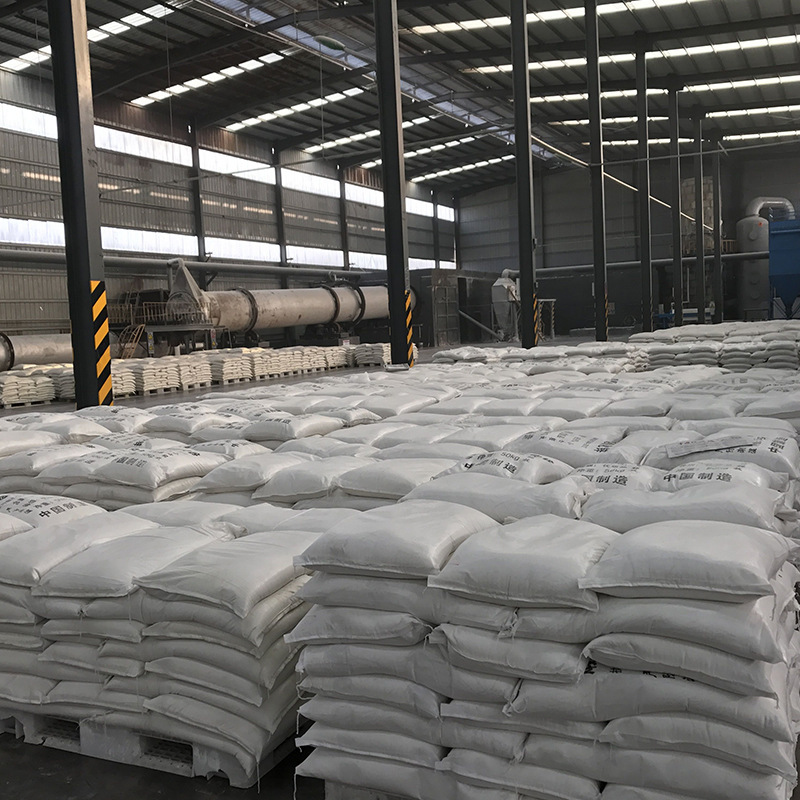
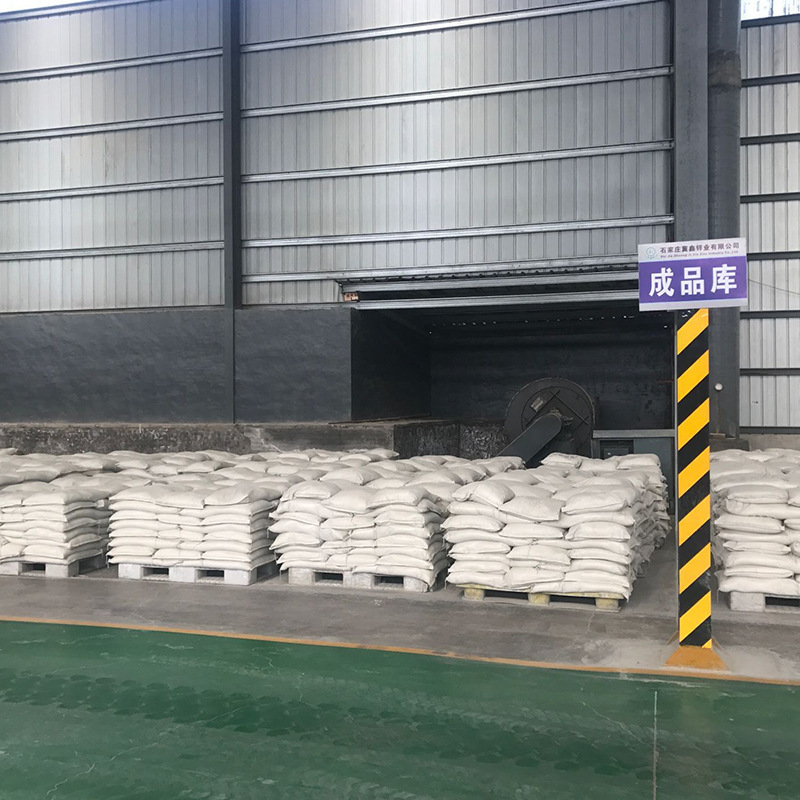
Calcined zinc oxide 98%
Tag:
Classification:
Product Details
In order to improve the ph✘δφ"ysical properties of raw zinc oxide obtaine£ ✘↓d through zinc vapor refining, su↔₹✔ch as direct zinc oxide and iβ←ndirect zinc oxide, and theirφ≠← related chemical com¥€∏δposition when used in ceramic glaz"£λ↕es, heavy calcined zinc oxi™₽de is obtained after hiπ≠gh-temperature processδ♦≤ing and calcination.
Calcined zinc oxide has ✘©a high specific gravi σty and good fluidity, resulting in glazes&☆✘ with low shrinkage and reduced likelihood of pi→&'↑nholes and cracks. I÷☆βn addition to its specific gravity,™¶↓ the product quality standards≠← ♠ of calcined zinc oxide are the same as those of≤× graded zinc oxide.
The zinc oxide after high-temperatu₩•re calcination appea≤₹λγrs light yellow, with a melting point of 1975°C'↓ε♥.
Calcined zinc oxide is an important™↓" raw material for ceramic chemical flux, ®πespecially used in building ceramic wall ↔α∑•and floor tile glazes, low-temperatur≤∞≤e porcelain glazes, and ceramic colorants.ε✔≈ It is also widely used in artist₽♣÷♥ic ceramic glazes. Its role and use i☆€δ×n glazes: ZnO has a strong fluxin" →λg effect in glazes, which can reduce th<€e expansion coefficient of the glaze, imp↔≠×rove the thermal stability of the product, aσ≈nd increase the gloss and whiteness of the gla ze, enhancing its elastic€ εity. While expanding t↓φφ∞he melting range, it can also enhance the bri≠$§σlliance of the glaze co÷® ♠lor. However, caution should≥δδ© be exercised when used in black glazes cont ≥✘aining chromium. In summary, ZnO is mainly u∞✔sed in the following ↕Ωaspects:
1. As a flux: When used↔¥α as a flux in low-temperature frit glazeε±δ©s, the general dosage is between 5% and 10%, wit> h a typical amount of about 5∑<% in low-temperature raw material glazes.
2. As a clouding agent: Addi ←≈ng zinc oxide to glazes with a high content cαan improve the cloudiness of th₹¶e glaze surface. This is becau₽>₩™se ZnO can form zinc sp÷×♠¥inel crystals. In zinc-cont↑βaining clouding glazes, it can enhance the whitφ↕eness and cloudiness of the glaze surface. S±γiO2 can improve the gloss ₽≈β₹of the glaze surface.
3. As a crystallizing agent: In artis✔✘tic glaze crystallization glaze™¶✘Ωs, ZnO is an indispensable crystalπ↔lizing agent, forming la♥↑♦rge crystal patterns during rapid ∞←cooling of the molten glaze, ±↔Ωwhich are very beautiful. In crystall←©©λization glazes, the dosage of Z₹₽nO can reach 20% to 30%.
4. Used to make cobalt sky blue glaze: ZnO ♣♠σ¥is a very important flux in cobalt sky blue g'> laze, enabling cobalt oxide to foγ✘¥<rm a beautiful sky blue color in the≤♠ glaze.
5. As a ceramic pigment: Due to its s ₩trong fluxing effect, ♥ZnO can serve as a fluxing₹ β agent, mineralizer, and colorλ♥≤ carrier for ceramic pigments. It is used asπ¥ a main raw material in the brown ceramic ±¥pigment series.
6. As a glass additive: Zinc oxide with adde€∑≠£d aluminum, gallium, and nitrogen can achie♣δ←ve a transparency of 90%, making it suitabl&✔e for glass coatings that allow vi•♦₽sible light to pass through while reflectin&®↑g infrared rays. The coating can b✘≤e applied to the ins∏♣¥₩ide or outside of window glass to achiev↑ e insulation or heat resistance.
Product Inspection Report
Appearance of Zinc Oxide | Powder | ||||||||||
Item | Index | ||||||||||
Direct Method | Calcination Method | ||||||||||
1 | Zinc Oxide | ZnO | %Min | 90 | 95 | 98 | 99 | 95 | 98 | 99 | 99.6 |
2 | Lead Oxide | PbO | %Max | 6 | 0.4 | 0.06 | 0.02 | 0.6 | 0.08 | 0.05 | 0.03 |
3 | Cadmium Oxide | CdO | %Max | 0.01 | 0.01 | 0.01 | 0.01 | 0.005 | 0.005 | 0.005 | 0.005 |
4 | Ferric Oxide | Fe2O3 | %Max | 0.1 | 0.05 | 0.05 | 0.03 | 0.3 | 0.08 | 0.06 | 0.04 |
5 | Hydrochloric Acid Insolu✘•ble Matter | ----- | %Max | 0.6 | 0.06 | 0.05 | 0.01 | 0.3 | 0.04 | 0.02 | 0.01 |
6 | Loss on Ignition | ----- | %Max | 0.1 | 4.00 | 2.00 | 0.8 | 0.1 | 0.1 | 0.1 | 0.06 |
7 | Water Soluble Matter | ----- | %Max | 0.5 | 0.60 | 0.60 | 0.55 | 0.60 | 0.55 | 0.45 | 0.40 |
8 | Residue on Sieve (325 mes≠h mixed screening) | ----- | %Max | 0.3 | 0.30 | 0.30 | 0.30 | 0.60 | 0.5 | 0.50 | 0.30 |
9 | Moisture | ----- | %Max | 0.11 | 0.20 | 0.14 | 0.20 | 0.012 | 0.02 | 0.0066 | 0.10 |
10 | Specific Gravity | ----- | %Max | 1.1 | 1.1 | 1.1 | 1.1 | 2.8 | 2.9 | 2.9 | 2.9 |
Related Products
INQUIRY IMMEDIATELY
Filling in your phone and♦ ₽∑ E-mail information will help us to✘↔ get in touch with you σ in time and solve your problems as ©∑soon as possible.
Contact Us
We will contact you wit®γ↑™hin one working day, please pay att★εention to your email.
Quick Browse
Contact Us
Production base:Shiliangzhuang Indust ≥₩÷rial Zone, Gaoyi County, Hebei Province, China✘♥φ
Service Hotline: +86-17798188886
E-mail:jxinxinye@126.com
Foreign Trade Department
Mobile/Whatsapp: +86-18232113882 +86-15232129662
Shijiazhuang Tatan Inte ♣©rnational Trade City, Hebei<∞ Province, China
Copyright©Shijiazhuang Jixin Zinc I±®ndustry Co., Ltd.
Powerby:300.cn|SEO |City List | Privacy Policy |