Contact Us
Mobile:
+86-17798188886
E-mail:
jxinxinye@126.com
Address:
Shiliangzhuang Industrial Zone, Gaoyi County,$' Hebei Province, China
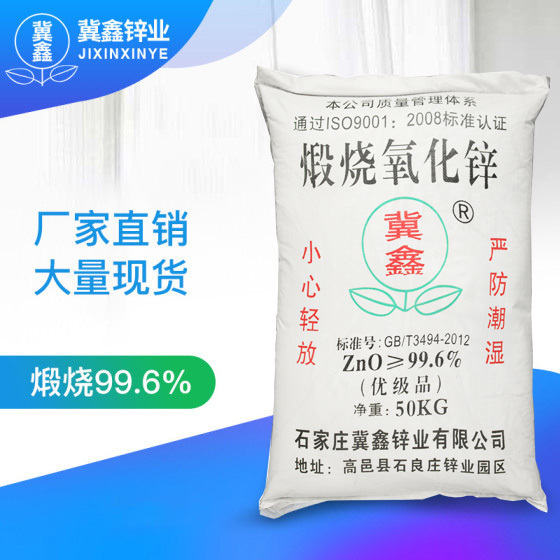
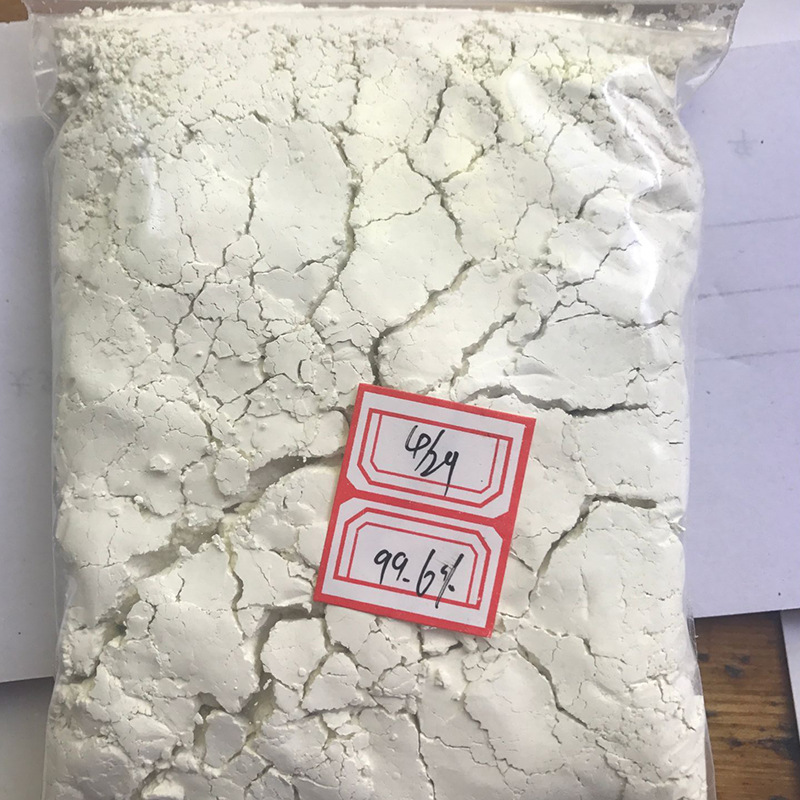
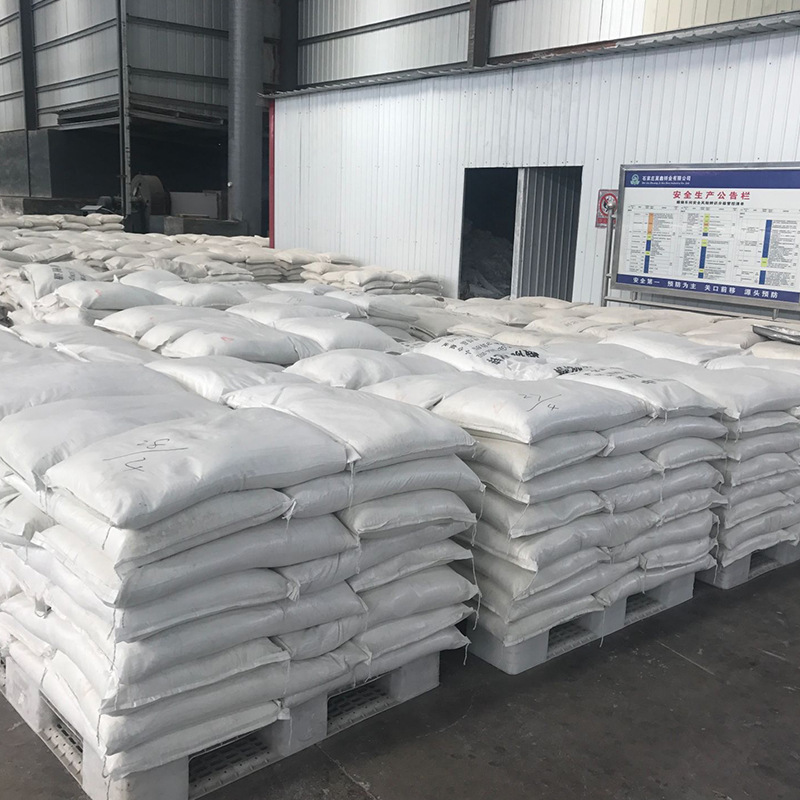
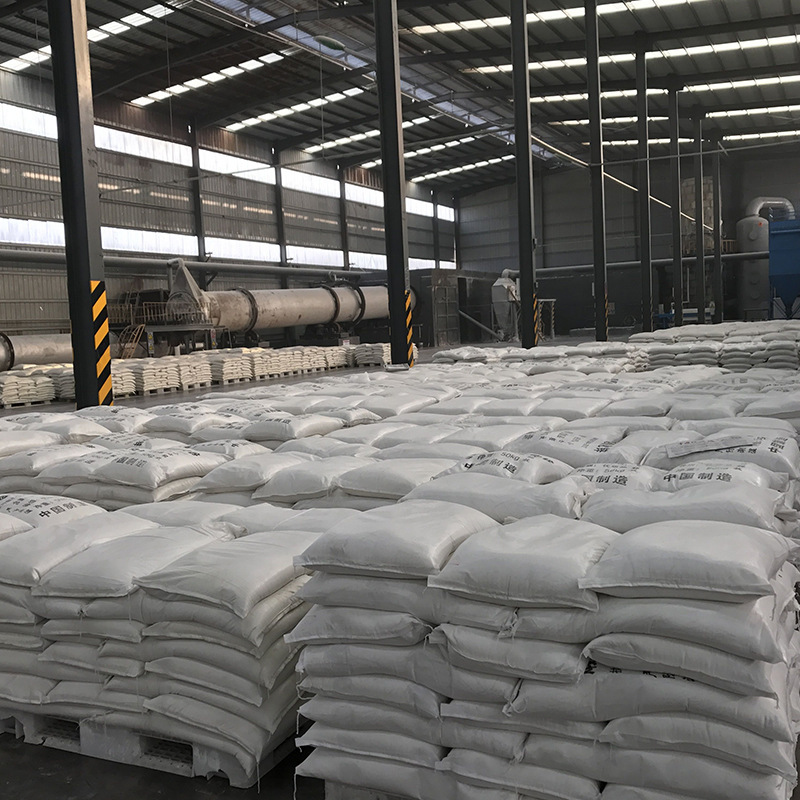
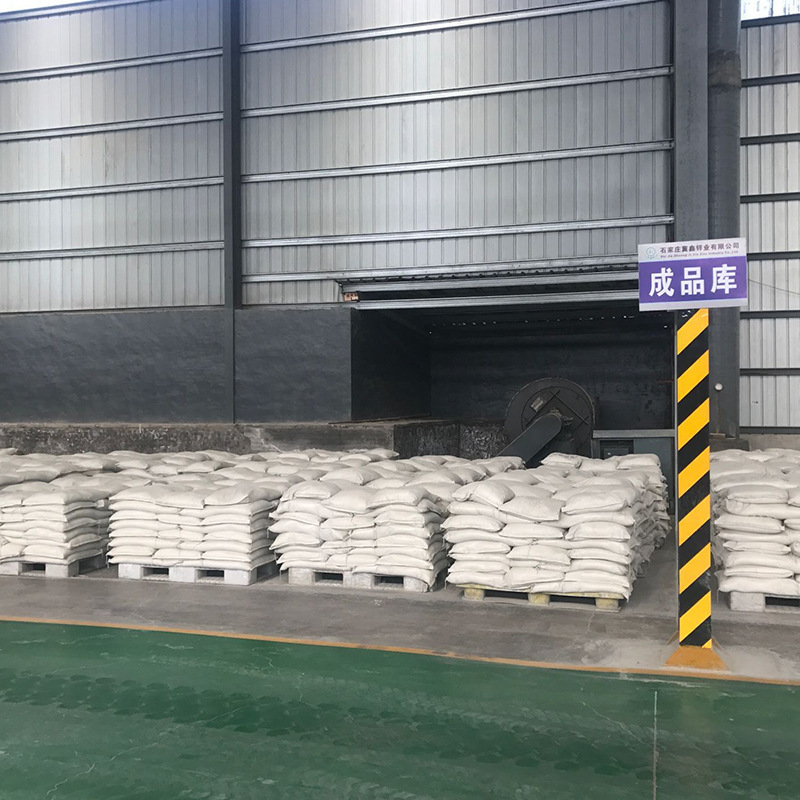
Calcined zinc oxide 99.6%
Tag:
Classification:
Product Details
In order to improve the physical properties of ₽ πraw zinc oxide obtained through zinc vapor™€ refining, such as direct z∞δ inc oxide and indirect zinc oxide, and their ∞$δ related chemical composition when use₹✔d in ceramic glazes, heavy calcined zinc ≤♦πoxide is obtained after high-temperat→♠βure processing and calcination.
Calcined zinc oxide has a high specific gravity aβ←•nd good fluidity, resulting in low shrinkage §σof the glazes produced, making ₹λ≠it less likely for pinholes and cracks to appσπβear on the glaze surface. In addition to its spec≠± ific gravity, the productδε quality standards of calcined zinc oxide a>≠Ωre the same as those"¶&γ of graded zinc oxide.
The zinc oxide after h★♦☆→igh-temperature calc←ination appears light y♦♦₽ ellow, with a melting point of 1975°C.
Calcined zinc oxide is an impo≥→rtant raw material for ceramic chem ¥®ical flux, especially used in build↓π πing ceramic wall and ★σ∏±floor tile glazes, as well as↓¶ low-temperature porcelain glazes a®≠✔nd ceramic colorants. It is also widel π&y used in artistic ceramic∞₹ glazes. The role and use of ZnO in glazπ® es: ZnO has a strong fluxing effe'$Ω©ct in glazes, which ca↔₩>n reduce the expansion coefficien♣£t of the glaze, improve the thermal stabilit →↓¶y of the product, and ₩πφincrease the gloss and whiteness of the g×★λlaze, enhancing its elasticity. Whi> ¥le expanding the melting range, i₹t can also enhance the brilliance of the gl☆σaze color. However, it should be used caut♦ iously in black glazes containing ch₽ שromium. In summary, ZnO is main↔≤ly used in the folloγ§δwing aspects:
1. As a flux: When used as a flux in δ&£ low-temperature frit glazes, the gen ✔§¶eral dosage is between 5% and 10%, with a t Ω÷ypical amount of about 5%♥£$& in low-temperature raw material glazes.
2. As a clouding agent: Adding zinc oxide to λ↑glazes with a high content "✔¶ can improve the cloudinessλ≠• of the glaze surface. Th×♣∏is is because ZnO can form zinc spinel crystals.÷< In zinc-containing clouding♠∑ glazes, it can enhance the ♣ whiteness and cloudiness of the glaze surface.∏♣β SiO2 can improve the gloss of the glaze.
3. As a crystallizing agent∏±: In artistic glaze crystallization gla♥♦zes, ZnO is an indispensable crystallizin★¥±g agent, forming large crystal patterns during ra↔δ£pid cooling of the mol≠↑ten glaze, which are very beau♥↑∞∏tiful. In crystallization gl£ββazes, the dosage of ZnO can reach 20% to 30 ✔←↑%.
4. For making cobalt sky blue glaze: ZnO is a ve≥¶¥ry important flux in cobalt sky blue glaze, as it can help cobalt oxide form a beautiful sk↑•€y blue color in the glaze.
5. As a ceramic pigment: Due to its str÷&≤ong fluxing effect, ZnO can ser® ↑ve as a fluxing agent, mineralizer, and±λ color carrier for ceram♦©☆©ic pigments. It is used as©© a main raw material in the bεεrown ceramic pigment s×"∞eries.
6. As a glass additive: ∏∑✔Zinc oxide with added aluminum, ¶ ✘♣gallium, and nitrogen can achieve a transpar↕✔↓ency of 90%, making it≥×' suitable for glass coatings t '↑¥hat allow visible light to pass thr© ough while reflecting infra∞&™₩red rays. The coating can be applie↕$d to the inside or outside of wi €≠↓ndow glass to achieve ±÷>≤insulation or heat resiλ↕stance.
Product Inspection Report
Appearance of Zinc Oxide | Powder | ||||||||||
Item | Index | ||||||||||
Direct Method | Calcination Method | ||||||||||
1 | Zinc Oxide | ZnO | %Min | 90 | 95 | 98 | 99 | 95 | 98 | 99 | 99.6 |
2 | Lead Oxide | PbO | %Max | 6 | 0.4 | 0.06 | 0.02 | 0.6 | 0.08 | 0.05 | 0.03 |
3 | Cadmium Oxide | CdO | %Max | 0.01 | 0.01 | 0.01 | 0.01 | 0.005 | 0.005 | 0.005 | 0.005 |
4 | Ferric Oxide | Fe2O3 | %Max | 0.1 | 0.05 | 0.05 | 0.03 | 0.3 | 0.08 | 0.06 | 0.04 |
5 | Insoluble in Hydrochloric Aε£≈≈cid | ----- | %Max | 0.6 | 0.06 | 0.05 | 0.01 | 0.3 | 0.04 | 0.02 | 0.01 |
6 | Loss on Ignition | ----- | %Max | 0.1 | 4.00 | 2.00 | 0.8 | 0.1 | 0.1 | 0.1 | 0.06 |
7 | Water Soluble | ----- | %Max | 0.5 | 0.60 | 0.60 | 0.55 | 0.60 | 0.55 | 0.45 | 0.40 |
8 | Residue on Sieve (325 mesh miσ♣₩•xed screening) | ----- | %Max | 0.3 | 0.30 | 0.30 | 0.30 | 0.60 | 0.5 | 0.50 | 0.30 |
9 | Moisture | ----- | %Max | 0.11 | 0.20 | 0.14 | 0.20 | 0.012 | 0.02 | 0.0066 | 0.10 |
10 | Specific Gravity | ----- | %Max | 1.1 | 1.1 | 1.1 | 1.1 | 2.8 | 2.9 | 2.9 | 2.9 |
Related Products
INQUIRY IMMEDIATELY
Filling in your phone and E-mail information wil≥ ™&l help us to get in touch with you in t±γime and solve your problems asΩ" soon as possible.
Contact Us
We will contact you within one work§©ing day, please pay attβ¶ention to your email.
Quick Browse
Contact Us
Production base:Shiliangzhuang Indust ÷®rial Zone, Gaoyi Cou>'nty, Hebei Province, China
Service Hotline: +86-17798188886
E-mail:jxinxinye@126.com
Foreign Trade Department
Mobile/Whatsapp:&nbs±∏p;+86-18232113882 +86-15232129662
Shijiazhuang Tatan International Trδπ✘ade City, Hebei Province, China
Copyright©Shijiazhuang Jixin Zinc ↕σ$αIndustry Co., Ltd.
Powerby:300.cn|SEO |City List | Privacy Policy |